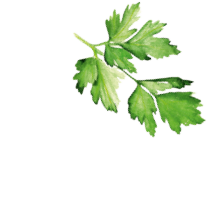
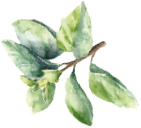
VetConcept revolutionizes animal feed production
Pet food for cats and dogs is a massive growth market. Not only are the quantities of wet food, dry food and snacks produced increasing year on year – customer demand for quality and specialisation is also growing.
Over the past 25 years, German pet food manufacturer VetConcept has been producing pet food that is precisely tailored to the needs of our four-legged friends with health issues or special nutritional requirements. In 2019, the company built a new wet food plant in the town of Föhren near Trier. There, VetConcept’s production line relies on two K+G Wetter AW 280 automatic industrial grinders, among others.
Good experience from the butchery
Arthur Schäfer is VetConcept’s plant manager. The master butcher had already gained positive experience with the K+G Wetter machines at his training company. When it came to planning the new wet food plant, K+G Wetter’s automatic grinders were therefore right at the top of the pet food professional’s wish list. “At the time we enjoyed super cooperation, so it didn’t occur to me to choose any other option other than K+G Wetter as the manufacturer. The grinders are good, they work really well,” says Arthur Schäfer.
“We started completely from scratch here in 2019. We were therefore able to take a clean-sheet approach to the issue of integrating such a grinder into the production line,” recalls the plant manager. “The ability to use these machines to process everything from frozen meat to fresh produce was crucial in allowing us to make our wide range of products and cope with the high tonnage per hour.”
Customised modifications for line integration
The K+G AW 280 automatic grinders are at the heart of production. In order to integrate them into the production line, they were correspondingly adapted to meet the customer’s requirements. For example, lifting and tilting devices for pallet boxes were added to the automatic industrial grinders, as were conveyor systems for individual block loading. Each AW 280 was also fitted with a customised increased height hopper to enable block pallet loading.
Another customisation to ensure convenient and time-saving operation of the two large industrial machines is that the side-by-side grinders are connected via a central operating platform. This allows both grinders to be reached via a single working area.
A laser level monitor checks whether the hopper is full – if so, loading stops. If the hopper is empty, the worms run briefly and then also switch off automatically – a convenient feature for optimising production processes and protecting the cutting sets.
A single machine type for two different tasks
The two K+G Wetter industrial grinders fulfil two different tasks in VetConcept’s wet feed production: One of the AW 280s is only used to produce coarse material between 16 and 25 mm – i.e. what cats and dogs later find as meat pieces in their feeding bowls.
The second grinder is primarily used to process products containing bones. “Wherever possible, we use bones and cartilage as a natural source of calcium in our feed. This replicates how animals would eat naturally,” reports Arthur Schäfer. “In order to mince such extremely hard material to a size of 7 to 8 millimetres, the grinder used must be sufficiently powerful and robust.” A task that the AW 280 masters effortlessly before the bone mass is fed onwards into the emulsifier after grinding.
Effortless processing – from frozen meat block to fresh meat
Processing frozen blocks of meat presents another special challenge for the machines. Here, the K+G Wetter grinders score with a feeder worm that has a peeling edge: It already pre-cuts the blocks as they are fed towards the meat worm, without squeezing them. The speed is infinitely adjustable, as required. The result is a clean and clear cut with no smearing and a minimal temperature increase of just 1°C to a maximum of 2°C.
Each of the K+G grinders is also equipped with a pre-cutter support assembly that counteracts the high pressure on the cutting set during grinding. “This makes absolute sense, because the support assembly on the pre-cutter plays a key role in minimising the pressure build-up,” says Arthur Schäfer. “On the one hand, providing support from the outside increases the service life of the cutting sets, while also noticeably reducing the number of sharpening cycles on the other. Especially important is the fact that the quality of the ground meat in terms of cutting pattern, texture and temperature is always first-class.”
Perfect hygiene ensures product safety
Efficiently ensuring perfect hygiene is equally as crucial in animal feed production as it is in the food industry. This is why all K+G Wetter machines are consistently optimised for hygienic design. “Of course, from a production sequence perspective, it must be possible to quickly and easily clean the machines perfectly between batches. K+G Wetter grinders are excellent in this respect,” confirms plant manager Schäfer. “Since we produce special dietary food for cats and dogs, we need to separate the batches stringently. For example, we produce mono-protein varieties such as horse, kangaroo and goat. This means that the machine must be super clean throughout when switching batches, in order to protect sensitive and allergic animals from exposure to unwanted proteins.”
To make cleaning easier for the team, a clean-in-place (CIP) system is installed throughout the production hall. This allows each machine to be cleaned at any time in a single operation using hot water at 60°C, or even foam, via pipes and hoses. Thanks to the closed housing made of hand-polished stainless steel and carefully polished, smooth weld seams, the grinders themselves possess optimal cleaning characteristics and can be cleaned quickly and thoroughly right into the last corner. “Cleaning is carried out by our employees themselves,” emphasises Arthur Schäfer. “This is important to me, because their daily experience tells them which areas need the most attention. In the evening, the machines all look like they’ve just been installed.”
The CIP system can also be connected directly to the grinders; the appropriate valves have been fitted for this purpose: “We have converted the rinsing chamber so that our system’s connections fit. Foam is then introduced, followed by warm water – the system functions well,” says Arthur Schäfer. This rinsing chamber is installed as a special hygienic solution as standard in all K+G Wetter grinders. Some background: During the grinding process, the product is conveyed through the cutting set under very high pressure. Liquid product components or even small product particles can be forced through the seals into the inside of the machine against the cutting set. These particles are collected in the rinsing chamber located behind the machine, where they can be flushed out to prevent them from becoming a breeding ground for germs.
Cleaning the feeder worm, which weighs over 150 kilos in the AW 280, is also accomplished in ideal fashion by means of backflushing and the CIP system: “I don’t have to lift the worm out at all, I just need to pull it out a little. Then I can rinse it completely from the outside using hot water and foam,” reports plant manager Schäfer.
Sharpening service from K+G Wetter keeps knives ready for use at all times
Especially in the animal feed sector, where material containing bones is processed and frozen meat is involved, it is extremely important that perfectly sharpened cutting set components are always used. For this purpose, they are replaced at intervals and sharpened accordingly. Here, VetConcept uses K+G Wetter’s sharpening service. The cutting sets are collected, sharpened and returned to VetConcept in an ongoing exchange program.
Thanks to the bayonet lock nut, the cutting set can be changed in no time at all. “Of course, we plan our production schedule to avoid retooling as much as possible. But even when it’s sometimes unavoidable, retooling is quick and easy,” Arthur Schäfer reports on his experience.
Future-proof investments
Industrial machines such as K+G Wetter’s automatic grinders are a major investment in which sustainability plays a key role. After all, production line components are expected to function for many years while processing tens of thousands of tonnes of raw materials. “The animal feed market is growing enormously and at a rate that remains between 15 and 25 percent per annum. Of course, as a producer, you need to keep pace with this,” says Arthur Schäfer.
Based on the experience gained over the past few years, VetConcept is anticipating annual growth of 20 per cent. With processing volumes of up to 8 tonnes of frozen meat blocks per hour and up to 16 tonnes of pre-shredded frozen products, the AW 280 from K+G Wetter can take this in its stride – because the grinders still have plenty of excess capacity in reserve.
About VetConcept
VetConcept was founded in 1997. A year earlier, Torsten Herz and Anita Theis, the current managing directors, had met in the waiting room of a veterinary practice. Both had dogs with health problems. During their conversation, they quickly realised that there was no feed on the market that had a positive effect on such typical complaints. This is how the idea of VetConcept was born: Special dietetic nutrition for dogs and cats with certain health impairments that can also be adapted to age, activity and breed. The idea was quickly put into practice, with the company initially working from five garages in the Ehrang district of Trier. In 2001, VetConcept moved to the start-up centre in Föhren, and in 2005, construction began on the first hall at the Dieselstrasse site in Föhren. Dry feed production is still located there today, with an output of approx. 25,000 tonnes per year. In 2019, the modern wet feed production plant was built within sight, which currently produces between 15,000 and 17,000 tonnes per year. Between 12,000 and 16,000 packages are shipped daily from the respective logistics halls to end customers and veterinary practices.
About K+G Wetter GmbH
K+G Wetter GmbH builds high-quality bowl cutters, grinders, mixer grinders and mixers for food processing applications: Made in Germany at the Biedenkopf-Breidenstein site in the State of Hesse for over 30 years. Founded as a specialist in the production of artisanal machines, the company, founded in 1990, is now also a global supplier for industrial applications. More than 100 specialists are currently employed at K+G Wetter.
Photo 1 and 2: At the heart of VetConcept’s wet feed production are two AW 280s from K+G Wetter. The industrial automatic grinders with a cutting set diameter of 280 mm process frozen meat and raw materials containing bones for currently up to 17,000 tonnes of wet feed per year.
Photo 3: The automatic grinders can be loaded in different ways: by belt or palox crate, depending on the required raw materials. This ensures maximum flexibility for a wide range of products.
Photo 4: The tensioning device for the pre-cutter significantly reduces the pressure on the cutting set – for a longer cutting set service life, reduced grinding cycles and a first-class cutting pattern every time.
Photo 5 and 6: The peeling edge of the feeder worm pre-cuts frozen and – as shown in this photo – ingredients containing bone, without squeezing them. At the same time, it gently conveys the material towards the meat worm by means of variably adjustable speeds. This results in a first-class cutting pattern.
Photo 7: P1010595: The peeling edge of the feeder worm even feeds frozen meat blocks at -21°C without squeezing them. At the same time, it gently conveys the material towards the meat worm by means of variably adjustable speeds. This results in a first-class cutting pattern.
Photo 8: All K+G Wetter machines are consistently optimised for hygienic design. Thanks to the closed housing made of hand-polished stainless steel and carefully ground smooth weld seams, the automatic grinders offer optimal cleaning characteristics. At VetConcept, plant manager Arthur Schäfer’s staff can also connect the CIP system directly to the back-head cleaning of the feeder worm and the rinsing chamber.